ایمنی صنعتی چیست؟ راهنمای جامع HSE از صفر تا صد + نکات کاربردی
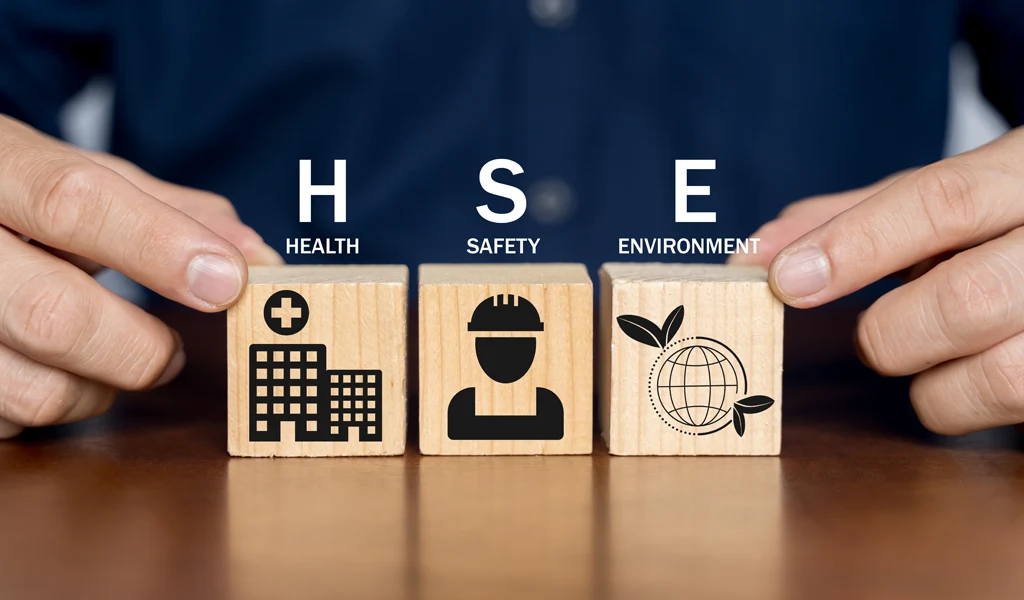
در این مقاله که با عنوان مرجع ایمنی صنعتی تهیه شده، قصد داریم به این پرسش پاسخ دهیم که چرا حوادث شغلی رخ میدهند؟
چرا هر سال هزاران نفر به دلیل بروز حوادث کاری جان خود را از دست میدهند یا دچار نقص عضو میشوند؟
آیا راهکاری برای کاهش یا جلوگیری از این حوادث وجود ندارد؟
آیا نمیتوان همزمان با پیشرفت صنعت، از تخریب محیط زیست جلوگیری کرد؟
پاسخ تمام این سؤالات در دانش HSE نهفته است؛ دانشی که رسالت آن جلوگیری از وقوع حوادث، کاهش شدت آسیبها و حفاظت از محیط زیست است.
در ابتدای این مقاله، مفاهیم پایهای ایمنی صنعتی را به زبان ساده توضیح میدهیم. این مفاهیم شامل ریسک، خطر، مخاطره و همچنین علل مستقیم، غیرمستقیم و ریشهای حوادث میشوند.
سپس، به بررسی هفت موضوع کلیدی در این حوزه میپردازیم که عبارتاند از:
- مدیریت آماری حوادث HSE
- روشهای اجرایی HSE
- عوامل زیانآور ارگونومیکی محیط کار
- ایمنی مواد شیمیایی
- ایمنی ماشینآلات صنعتی (مانند لیفتراک)
- سیستم برچسبگذاری و قفلگذاری (LOTO)
- تجهیزات کار در ارتفاع
اکنون، وارد نخستین بخش مقاله میشویم:
۱. آشنایی با مفاهیم پایه در ایمنی صنعتی
اصطلاح HSE از سه حرف اول واژههای Health (سلامتی)، Safety (ایمنی) و Environment (محیط زیست) تشکیل شده است. به همین دلیل، این حوزه را با عنوان “ایمنی صنعتی” نیز میشناسند؛ دانشی که به بررسی و اجرای فرایندهایی برای حفظ سلامت کارکنان، ایمنی تجهیزات و حفاظت از محیطزیست در محیطهای صنعتی میپردازد.
هدف اصلی ایمنی صنعتی، کاهش و پیشگیری از حوادث و آسیبهای ناشی از فعالیتهای صنعتی است. در این بخش، با مهمترین اصطلاحات و مفاهیم این حوزه آشنا خواهید شد:
۱-۱. تعریف ریسک و مدیریت ریسک
یکی از مفاهیم کلیدی در HSE، مفهوم “ریسک” و “مدیریت ریسک” است.
ریسک، به طور علمی، عبارت است از: تأثیر عدم قطعیتها بر اهداف سازمان.
مثلاً زلزله، یک عدم قطعیت است. شما نمیتوانید مانع وقوع آن شوید یا حتی زمان دقیق آن را پیشبینی کنید. حال، تأثیر احتمالی زلزله بر عملکرد سازمان، یک ریسک محسوب میشود.
مدیریت ریسک یعنی:
شناسایی این عدم قطعیتها، ارزیابی اثرات آنها و اتخاذ تدابیری برای کاهش یا حذف آنها.
بهعنوان نمونه، اگر برای احتمال وقوع آتشسوزی در محل کار خود، کپسول آتشنشانی تهیه کردهاید، یعنی مدیریت ریسک انجام دادهاید.
در این بخش، مفاهیم «درخت حوادث»، «علل مستقیم، غیرمستقیم و ریشهای حوادث»، «راهکارهای پیشگیری از حوادث» و تفاوت دقیق بین مخاطره (Hazard)، خطر (Danger) و ریسک (Risk) شرح داده شده. متن همچنان روان، تخصصی و وفادار به محتوای اصلیه.
۲-۱. درخت حوادث در ایمنی صنعتی
برای کاهش و کنترل حوادث، ابتدا باید آنها را بهدرستی طبقهبندی کنیم. یکی از روشهای مؤثر در این زمینه، استفاده از مدل «درخت حوادث» (Accident Tree) است.
در این مدل، دلایل بروز حوادث به سه گروه اصلی تقسیم میشوند:
- عوامل انسانی (طراحی نادرست، عدم نظارت، خطای بهرهبرداری، تصمیمگیری اشتباه)
- عوامل محیطی (شرایط آبوهوایی، وضعیت اجتماعی و اقتصادی)
- تجهیزات و مواد (نقص فنی، خرابی، شکست قطعات)
شناخت این دستهبندیها به تحلیل دقیقتر و پیشگیری مؤثرتر کمک میکند.
۳-۱. علل مستقیم، غیرمستقیم و ریشهای حوادث
در تحلیل حوادث، باید میان علل مستقیم، غیرمستقیم و ریشهای تمایز قائل شویم. برای روشنتر شدن این مفاهیم، به یک مثال واقعی توجه کنید:
فرض کنید راننده یک بلدوزر بدون توجه به محدودیتهای منطقه، اقدام به خاکبرداری میکند. در جریان این عملیات، لوله گاز شکسته و منجر به نشت گاز و در نهایت انفجار میشود.
در این حادثه، عوامل زیر قابل شناساییاند:
- علت مستقیم: برخورد بیل بلدوزر با لوله گاز.
- علل غیرمستقیم:
- وجود شرایط محیطی پرریسک
- نقص در اطلاعرسانی به راننده
- عدم رعایت قوانین ایمنی
- فقدان علائم هشداردهنده و حفاظها
- علل ریشهای:
- عدم ارزیابی صحیح ریسکها توسط پیمانکار
- ضعف در نظارت اجرایی
- آموزش ناکافی به کارکنان
- نداشتن دستورالعمل اجرایی ایمن
در بسیاری از موارد، حوادث پیچیدهتر از آن چیزی هستند که در نگاه اول به نظر میرسند.
۴-۱. راهکارهای پیشگیری از وقوع حوادث
دانش HSE فقط به تحلیل حوادث نمیپردازد، بلکه برای پیشگیری از آنها نیز راهکارهای کاربردی ارائه میدهد.
در برخی کشورها، واکنشها به حوادث اغلب سطحی و غیرمنطقی است (مانند اخراج یا جریمه فرد مقصر). این نوع برخوردها نهتنها باعث جلوگیری از تکرار حادثه نمیشوند، بلکه گاهی آن را پنهان هم میکنند.
در مقابل، راهکارهای اصولی شامل موارد زیر هستند:
- تدوین و اجرای الزامات جدید قانونی
- استفاده از فناوریهای روز برای کاهش خطای انسانی
- بهبود شرایط محیط کار و حذف خطرات شناساییشده
- بازنگری در استفاده از ماشینآلات و حذف تجهیزات ناایمن
واقعیت این است که هیچ حادثهای بیدلیل رخ نمیدهد؛ همیشه میتوان با شناسایی نشانهها، از آن جلوگیری کرد یا حداقل شدت آن را کاهش داد.
۵-۱. تفاوت مخاطره (Hazard)، خطر (Danger) و ریسک (Risk)
در زبان فارسی، واژگان Hazard، Danger و Risk معمولاً با کلمه “خطر” ترجمه میشوند. اما این سه مفهوم تفاوتهای مهمی با یکدیگر دارند:
مخاطره (Hazard)
مخاطره به هر چیزی اطلاق میشود که پتانسیل آسیبرسانی به انسان، محیط زیست، سرمایه یا اعتبار سازمان را دارد.
مثالهایی از مخاطره:
- اختلاف ارتفاع
- برق فشار قوی
- مواد شیمیایی
- ماشینآلات صنعتی مثل سنگ فرز، دریل یا دستگاه جوش
مخاطرات معمولاً قابل حذف نیستند، ولی میتوان خطر ناشی از آنها را مدیریت کرد.
خطر (Danger)
هر مخاطرهای که مهار نشده باشد، به یک خطر بالفعل تبدیل میشود.
برای مثال:
- سیم برق لخت و بدون پوشش
- دستگاه سنگ فرزی که فاقد قاب محافظ باشد
- کار با ابزارهای صنعتی بدون استفاده از تجهیزات ایمنی
نکته مهم: هر مخاطره میتواند چندین خطر داشته باشد و هر خطر، یک یا چند ریسک ایجاد کند.
ریسک (Risk)
ریسک به در معرض خطر قرار گرفتن اشاره دارد.
برای درک بهتر، به این مثال دقت کنید:
- سنگ فرز → مخاطره (Hazard)
- احتمال پرتاب براده به چشم → خطر (Danger)
- کارکردن بدون عینک ایمنی → ریسک (Risk)
حذف مخاطره در بسیاری از مواقع ممکن نیست؛ اما با استفاده از تجهیزات مناسب، میتوان خطر و ریسک ناشی از آن را به حداقل رساند.
📌 مثال دیگر:
- وجود کوسه در دریا = مخاطره
- حمله کوسه = خطر
- شنا کردن در محدوده کوسهها = ریسک
در این بخش با مفاهیم پایه و کلیدی دانش HSE آشنا شدیم. در ادامه، به سراغ فصل دوم مقاله میرویم:
✅ اگر این بخش مورد تأییدته، ادامه بازنویسی مقاله از فصل دوم یعنی «مدیریت آماری حوادث HSE» رو شروع میکنم.
آیا ادامه بدم و فایل Word این بخش رو هم برات بفرستم؟
۲ مدیریت آماری حوادث HSE در مرجع ایمنی صنعتی
تصور کنید که شما بهتازگی به عنوان مسئول HSE یک کارخانه استخدام شدهاید. بودجه مشخصی به شما اختصاص داده شده و از شما خواستهاند با استفاده از آن، آمار حوادث را کاهش دهید.
اولین قدم، شناسایی دقیق ریسکها، خطرات و مخاطرات موجود در محیط کار است.
در مرحله بعد، باید با بهرهگیری از ابزارها و تکنولوژیهای روز و همچنین برگزاری جلسات Root Cause Analysis (تحلیل ریشهای علل)، برای هرکدام از این موارد راهحل مناسبی ارائه کنید.
در این مسیر، اطلاعات آماری حوادث گذشته در همان مجموعه یا صنایع مشابه، به شما کمک شایانی خواهد کرد. چرا که بودجه شما محدود است و نمیتوانید همه خطرات را بهیکباره حذف کنید. در نتیجه باید بتوانید:
- حوادث را اولویتبندی کنید
- ریسکهای با اولویت بالاتر را در اولویت کاهش یا حذف قرار دهید
اما این اولویتبندی بر چه اساسی انجام میشود؟ دو فاکتور کلیدی را باید مدنظر قرار دهید:
۱-۲ هزینه رفع خطرات و مخاطرات
برخی خطرات را میتوان با هزینه بسیار کم حذف کرد، در حالی که برای مقابله با برخی دیگر، نیاز به سرمایهگذاری قابل توجهی است.
هنر یک کارشناس HSE این است که با کمترین هزینه، بیشترین کاهش در خطرات (Danger) و مخاطرات (Hazard) را ایجاد کند.
نمونه واقعی:
تصور کنید ستونی در محیط کارخانه باعث بروز حوادث متعدد شده است؛ مثلاً برخورد سر افراد یا ماشینآلات با آن.
برای رفع این خطر چند راهکار مطرح شده بود:
- حذف کامل ستون با محاسبات مهندسی و ایجاد دو ستون تقویتی جایگزین
- قرار دادن پدهای ضربهگیر نرم اطراف ستون
- تغییر مسیر عبور کارگران
- نصب تابلو و علائم هشدار
در نهایت، پوشاندن ستون با فوم ضربهگیر بهعنوان راهکاری کمهزینه و مؤثر انتخاب شد.
نکته مهم اینجاست که راهکار منتخب، علاوه بر کاهش خطر، امکان باقیمانده بودجه برای رفع سایر ریسکها را هم فراهم میکند.
۲-۲ بررسی آمار حوادث اتفاقافتاده
عامل دیگری که در تصمیمگیری برای اولویتبندی اهمیت دارد، بررسی آماری حوادث قبلی است.
بهطور منطقی، باید ابتدا سراغ خطراتی برویم که بیشتر باعث بروز حادثه شدهاند. در ادامه، مروری بر آمار رسمی حوادث در ایران خواهیم داشت:
۱) بیشترین حوادث شغلی ایران در کدام صنایع اتفاق میافتد؟
بیشترین حوادث شغلی ثبتشده در ایران، به صنعت ساختمان و ساختوساز مربوط میشود.
مثال:
اگر در پروژه ساخت پالایشگاه حادثهای رخ دهد، در آمار صنعت ساختمان ثبت میشود. اما اگر در حین بهرهبرداری و اورهال همان پالایشگاه حادثهای رخ دهد، آن را در صنعت نفت و گاز طبقهبندی میکنند.
۲) رایجترین نوع حادثه در ایران چیست؟
سقوط از ارتفاع، شایعترین حادثه شغلی در کشور است.
بسیاری تصور میکنند که فقط سقوط از ارتفاع بالا (مثلاً بیش از ۵ متر) خطرناک است، اما سقوط از ارتفاعهای کم (مثلاً ۸۰ سانتیمتر یا ۱.۵ متر) نیز میتواند منجر به آسیبهای جدی شود.
طبق استانداردهای ایمنی، هر فعالیتی در ارتفاع بیش از ۱۲۰ سانتیمتر، جزو کار در ارتفاع محسوب میشود و نیازمند رعایت نکات ایمنی خاص است.
۳) آسیبدیدگان حوادث شغلی در چه بازه سنی هستند؟
بر اساس آمار، اغلب آسیبدیدگان حوادث شغلی، در بازه سنی ۲۶ تا ۴۴ سال قرار دارند. یعنی افرادی در سنین کاری فعال.
۴) آیا سابقه کاری در نرخ حوادث تأثیر دارد؟
بله. جالب است بدانید دو گروه بیشترین میزان حادثه را تجربه میکنند:
- افراد تازهکار و بیتجربه
- افراد باسابقه و ماهر
افراد تازهکار معمولاً به دلیل عدم آگاهی از خطرات یا نداشتن مهارت کافی دچار حادثه میشوند.
در مقابل، افراد با تجربه بالا ممکن است به دلیل اعتمادبهنفس زیاد یا عادیانگاری شرایط، نکات ایمنی را نادیده بگیرند.
۵) تفاوت آماری با دیگر کشورها
نوع صنعت هر کشور بر آمار حوادث آن تأثیر دارد.
مثلاً در آمریکا، صنعت کشاورزی به دلیل گستردگی، بیشترین آمار حوادث را دارد. این به معنی ضعف ایمنی آن بخش نیست، بلکه به گستره فعالیت و تعداد شاغلان آن مربوط است.
در نتیجه:
- برای فعالیت در حوزه ایمنی ایران، باید تمرکز روی صنعت ساختوساز باشد
- در آمریکا، تمرکز اصلی روی کشاورزی است
- و در هر سازمان، بررسی آمار داخلی بسیار مهم است
۳ روشهای اجرایی HSE
تا اینجای مقاله، بیشتر با مفاهیم تئوری ایمنی صنعتی و HSE آشنا شدیم. از این بخش به بعد، وارد فاز عملیاتی میشویم. یعنی نحوه پیادهسازی این مفاهیم تئوری در محیط کار با استفاده از تکنیکها، استانداردها و سیستمهای مدیریتی.
۱-۳ چرخه دمینگ (PDCA)
یکی از تکنیکهای پرکاربرد در مدیریت HSE، چرخه دمینگ یا چرخه PDCA است.
PDCA از چهار مرحله زیر تشکیل شده:
- Plan (برنامهریزی): تعیین اهداف ایمنی، شناسایی ریسکها و تدوین راهکارها
- Do (اجرا): پیادهسازی راهکارها و برنامهها
- Check (بررسی): ارزیابی نتایج اجرای اقدامات
- Act (اقدام اصلاحی): اصلاح فرایندها و اقدامات برای بهبود مستمر
این چرخه به ما کمک میکند تا بهصورت پیوسته، وضعیت ایمنی را در سازمان رصد و بهبود دهیم.
چرخه دمینگ فقط مخصوص HSE نیست و در سایر سیستمهای مدیریتی مانند کیفیت و بهرهوری نیز استفاده میشود.
۲-۳ استانداردهای HSE و ممیزی
در هر حوزه صنعتی یا تخصصی، یکسری استاندارد فنی و سیستمی وجود دارد. در حوزه ایمنی، این استانداردها نقش حیاتی ایفا میکنند.
بهعنوان مثال، وقتی میگویند سازمانی موفق به دریافت گواهینامه ISO 14001 شده، به این معناست که آن سازمان در ممیزی مربوط به الزامات زیستمحیطی، تأیید شده است.
اما ممیزی چگونه انجام میشود؟
- فرد یا نهادی بهعنوان ممیز از سازمان بازدید میکند
- با استفاده از مصاحبه، بررسی مستندات و مشاهده محیط کاری، انطباق فعالیتها با استاندارد را ارزیابی میکند
- اگر عملکرد سازمان با الزامات استاندارد تطابق داشته باشد، گواهی مربوطه صادر میشود
استانداردها در حوزه HSE به دو دسته کلی تقسیم میشوند:
- استانداردهای داخلی: معمولاً الزامی هستند
- استانداردهای بینالمللی: الزامآور نیستند مگر در پروژههای بینالمللی یا صادراتی
برخی کشورها، استانداردهای داخلی خود را بر پایه استانداردهای جهانی تنظیم میکنند.
۳-۳ سیستم مدیریت HSE-MS
یکی از مفاهیم کلیدی در ایمنی صنعتی، مفهوم HSE-MS یا سیستم مدیریت HSE است.
برخی افراد تصور میکنند HSE-MS یک استاندارد رسمی است، اما اینطور نیست.
HSE-MS یک الگو یا مدل مدیریتی است که از استانداردها و تکنیکهای مختلف بهره میگیرد و هدف آن، ایجاد ساختاری منظم برای مدیریت مسائل بهداشتی، ایمنی و زیستمحیطی است.
این سیستم بیشتر در صنایع بزرگ، بهویژه حوزههای نفت، گاز و پتروشیمی کاربرد دارد.
مؤلفههای اصلی HSE-MS شامل موارد زیر هستند:
- خطمشی ایمنی و زیستمحیطی
- اهداف و شاخصهای قابل اندازهگیری
- برنامهریزی عملیاتی
- مدیریت ریسک
- آموزش و صلاحیت نیروی انسانی
- مدیریت بحران
- ممیزی داخلی و بازنگری مدیریتی
در این بخش از مقاله، با سه رکن مهم اجرایی در HSE آشنا شدیم: چرخه بهبود مستمر دمینگ، استانداردها و سیستم مدیریت HSE-MS.
✅ در ادامه مقاله، وارد فاز اجراییتر خواهیم شد و موضوعاتی مانند ایمنی مواد شیمیایی، ایمنی لیفتراک، ارگونومی محیط کار و … را بررسی میکنیم.
۴ عوامل زیانآور ارگونومیکی محیط کار
در محیطهای کاری، عوامل زیانآور متعددی وجود دارند که میتوان آنها را در دستههای مختلفی همچون عوامل فیزیکی، شیمیایی، ارگونومیکی، روانی و بیولوژیکی طبقهبندی کرد.
در این بخش، تمرکز ما بر روی عوامل ارگونومیکی است که تأثیر مستقیم بر سلامت فیزیکی کارکنان، بهویژه در بلندمدت، دارند.
ارگونومی چیست و چرا اهمیت دارد؟
ارگونومی به علم تطبیق ابزار، محیط کار و شرایط کاری با ویژگیهای فیزیکی و روانی انسان گفته میشود. هدف آن، افزایش بهرهوری و کاهش آسیبهای جسمی و ذهنی افراد در حین انجام کار است.
در محیط کار، ابزارآلات و ماشینآلات باید بهگونهای طراحی شوند که فشار غیرعادی به مفاصل، عضلات و ستون فقرات وارد نکنند.
مثالهایی از ابزارهایی که باید ارگونومیک باشند:
- موس و کیبورد کامپیوتر
- میز و صندلی اداری
- ابزارهای دستی مانند پیچگوشتی یا آچار
- صندلی و فرمان خودرو
- نوار نقاله، دستگاههای صنعتی، نردبانها و ایستگاههای کاری کارخانهای
اگر این ابزارها مطابق با حالت طبیعی بدن انسان طراحی نشده باشند، فرد ممکن است در بلندمدت دچار اختلالات عضلانی-اسکلتی شود.
نقش کارشناس HSE در ارگونومی محیط کار
کارشناس HSE باید فقط به تذکر دادن بسنده نکند! بلکه وظیفه اصلی او:
- شناسایی عوامل ارگونومیکی ناسازگار با بدن انسان
- تغییر طراحی ایستگاههای کاری، ابزارها و نحوه انجام کار برای رفع آنها
- آموزش صحیح به پرسنل برای استفاده درست از تجهیزات
یک مثال ملموس
کارگری را تصور کنید که روزانه چندین ساعت با ابزار ارتعاشدار (مثلاً دریل یا سنگ فرز) کار میکند. اگر طراحی دسته ابزار، نحوه ایستادن، موقعیت دست یا محل کار با شرایط فیزیکی انسان تطابق نداشته باشد، بهمرور دچار آسیب خواهد شد.
در این حالت، اقدامات ارگونومیکی مثل:
- استفاده از دسته ضد لرزش
- ایجاد سطح کار با ارتفاع مناسب
- آموزش نحوه صحیح نگهداشتن ابزار
- یا حتی تغییر چرخه کاری برای استراحت عضلات
میتوانند از بروز آسیبهای شغلی جلوگیری کنند.
🔍 خلاصه فصل:
- ارگونومی یعنی طراحی کار و ابزار متناسب با بدن انسان
- ابزارهای ناسازگار با بدن، باعث آسیبهای تدریجی و مزمن میشوند
- کارشناس HSE باید با تحلیل شرایط کاری و اصلاح طراحی، سلامت فیزیکی کارکنان را تضمین کند
۵ ایمنی مواد شیمیایی
ایمنی مواد شیمیایی یکی از حیاتیترین بخشهای دانش HSE محسوب میشود. این موضوع در صنایعی که با مواد شیمیایی سر و کار دارند، از اهمیت دوچندان برخوردار است.
مواد شیمیایی میتوانند باعث سوختگی، مسمومیت، اختلالات تنفسی، آلودگی محیط زیست، و حتی حوادث انفجاری و آتشسوزی شوند. بنابراین شناخت، استفاده صحیح، نگهداری اصولی و واکنش سریع در شرایط اضطراری کاملاً ضروری است.
در این فصل، به سه حوزه مهم مرتبط با ایمنی مواد شیمیایی میپردازیم:
۱-۵ نگهداری اصولی مواد شیمیایی
هر ماده شیمیایی، شرایط خاصی برای نگهداری دارد (مانند دما، رطوبت، نور و تهویه).
اگر این شرایط رعایت نشود:
- خواص شیمیایی ماده ممکن است تغییر کند
- خطرات آن افزایش مییابد
- حتی بدون استفاده، ماده میتواند حادثهساز شود
🔸 بهعنوان مثال:
اگر در برگه اطلاعات ایمنی (MSDS) یک ماده قید شده که باید در دمای ۱۰ تا ۵۰ درجه سانتیگراد نگهداری شود، اما آن را در دمای انبار ۶۰ درجه نگهداری کنید، احتمال نشت، انفجار یا کاهش کارایی آن وجود دارد.
📌 نکته مهم:
کارشناس HSE باید بهصورت مستمر، شرایط نگهداری مواد شیمیایی را بررسی کرده و آنها را با استانداردهای درجشده در MSDS تطبیق دهد.
۲-۵ کمکهای اضطراری در مواجهه با مواد شیمیایی
با وجود رعایت نکات ایمنی، باز هم امکان بروز حادثه وجود دارد. در چنین شرایطی، سرعت و دقت در واکنش اضطراری حیاتی است.
مهمترین تجهیزات در این زمینه عبارتاند از:
✅ چشمشور (Eye Wash Station)
- برای شستوشوی سریع چشمها هنگام پاشیدن مواد شیمیایی
- باید بهصورت فوری و به مدت حداقل ۲۰ دقیقه مورد استفاده قرار گیرد
- کارکنان باید نحوه استفاده از آن را آموزش دیده باشند
✅ دوش اضطراری (Safety Shower)
- برای شستوشوی مواد شیمیایی از روی پوست
- در آزمایشگاهها و کارگاههایی که احتمال تماس مستقیم با مواد شیمیایی وجود دارد، نصب آن الزامی است
🔺 آموزش استفاده صحیح از این تجهیزات، از الزامات HSE در هر سازمانی است.
۳-۵ تجهیزات حفاظت فردی (PPE) در برابر مواد شیمیایی
استفاده از تجهیزات حفاظت فردی نهتنها یک الزام قانونی بلکه یک اصل حیاتی برای جلوگیری از آسیبهای شیمیایی است.
⚠️ نکات مهم در استفاده از PPE:
- انتخاب صحیح تجهیزات:
مثلاً استفاده از کفش ایمنی فولادی در آزمایشگاه شیمیایی مناسب نیست؛ بلکه باید از کفش مقاوم در برابر مواد شیمیایی استفاده شود. - تاریخ انقضا:
بیشتر تجهیزات ایمنی مانند ماسکها، دستکشها، فیلترها و کلاههای ایمنی دارای تاریخ انقضا هستند. حتی اگر استفاده نشده باشند، پس از مدتی خاصیت حفاظتی خود را از دست میدهند. - باورهای غلط:
برخی کارکنان فکر میکنند چون بوی مواد شیمیایی مثل بنزین را احساس نمیکنند، بدنشان به آنها عادت کرده است!
اما واقعیت این است که بدن هیچگاه به مواد شیمیایی عادت نمیکند و آسیبهای ناشی از آن بهمرور ایجاد میشود.
🎯 جمعبندی فصل:
- شرایط نگهداری، استفاده و دفع مواد شیمیایی باید مطابق استانداردهای بینالمللی باشد
- تجهیزات اضطراری مانند چشمشور و دوش ایمنی باید در دسترس و آماده استفاده باشند
- استفاده از PPE باید متناسب با نوع ماده و طبق استانداردهای بهروز انجام شود
۶ ایمنی لیفتراک در محیطهای صنعتی
در چارچوب کنترلهای عملیاتی HSE، ایمنی ماشینآلات صنعتی اهمیت ویژهای دارد.
در این بین، لیفتراکها به دلیل کاربرد گسترده و آمار بالای حوادث، بهعنوان یکی از پرریسکترین تجهیزات شناخته میشوند.
طبق آمار، سالانه حدود ۸۵ تا ۱۰۰ نفر فقط در آمریکا به دلیل حوادث مرتبط با لیفتراک جان خود را از دست میدهند. این آمار در سایر کشورها نیز نگرانکننده است.
چرا لیفتراکها خطرناک هستند؟
برخلاف ظاهر سادهشان، لیفتراکها ماشینهایی با ریسک بالا محسوب میشوند. مهمترین دلایل این خطر عبارتاند از:
- میدان دید محدود راننده
- کنترل دشوار و عدم تعادل در بارهای سنگین یا نامتقارن
- پایداری کم هنگام دور زدن یا شیبها
- شتاب و توقف ناگهانی در فضاهای شلوغ
وظایف کارشناس HSE در ایمنی لیفتراک
- آموزش تخصصی به رانندگان لیفتراک:
نحوه رانندگی، بارگیری ایمن، نحوه دور زدن و ترمزگیری باید آموزش داده شود. - آگاهسازی سایر پرسنل:
کارکنانی که در محدوده تردد لیفتراک کار میکنند باید از زاویه دید محدود راننده و خطرات تردد لیفتراک مطلع باشند. - جداسازی مسیر تردد افراد و لیفتراکها:
تا حد امکان، محل تردد لیفتراک باید از محل رفتوآمد پرسنل جدا شود. در غیر این صورت، احتمال برخورد و تصادف وجود دارد.
مثال واقعی از حادثه لیفتراک
در یکی از کارگاهها، به دلیل دید محدود راننده، لیفتراک با یکی از کارکنان برخورد کرده و باعث آسیب شدید شد. بررسیها نشان داد:
- مسیر تردد پرسنل و لیفتراک مشترک بود
- آموزش کافی درباره خطرات داده نشده بود
- هیچگونه علامت هشدار یا جداکننده فیزیکی در محل وجود نداشت
📌 نتیجه: با اجرای چند اقدام ساده، میتوانست این حادثه کاملاً قابل پیشگیری باشد.
منابع آموزشی برای لیفتراک
- استفاده از ویدیوهای آموزشی ساده و تاثیرگذار برای رانندهها و پرسنل
- آموزش نکات ایمنی پایه مانند:
- بارگیری در مرکز ثقل
- سرعت مناسب
- توقف در محل مشخص
- هشداردهی در هنگام حرکت
🎯 جمعبندی فصل:
- لیفتراکها ماشینهایی با خطر بالقوه بالا هستند
- ضعف در دید، کنترل و جداسازی مسیرها مهمترین دلایل حوادث آنهاست
- آموزش، آگاهسازی و طراحی مسیرهای جداگانه، مهمترین اقدامات پیشگیرانه هستند
جمعبندی مقاله «مرجع ایمنی صنعتی»
ایمنی صنعتی بهعنوان یکی از زیرمجموعههای حیاتی HSE (ایمنی، بهداشت و محیط زیست)، نقش مهمی در پیشگیری از حوادث شغلی و ارتقای سلامت و بهرهوری نیروی کار ایفا میکند. این مقاله با هدف ارائه یک مرجع جامع و کاربردی، به بررسی مفاهیم کلیدی، روشهای اجرایی و ابزارهای ایمنی در محیطهای صنعتی پرداخته است.
در ابتدا، مفاهیم پایه ایمنی صنعتی شامل تعریف خطر، ریسک، حادثه و روشهای ارزیابی آنها تبیین شد. سپس با اتکا به آمارهای معتبر جهانی و ملی، تحلیلهایی در خصوص رایجترین علل حوادث شغلی، میزان بروز آنها و اثرات اقتصادی و انسانی این حوادث ارائه شد.
در بخش بعد، روشهای اجرایی ایمنی نظیر ارزیابی ریسک، اقدامات کنترلی، آموزشهای ایمنی، بازرسیهای دورهای و مستندسازی بررسی شدند. همچنین نقش ارگونومی در طراحی ایمن محیط کار، کاهش فشارهای فیزیکی و روانی بر کارکنان و پیشگیری از بیماریهای اسکلتی-عضلانی مورد تأکید قرار گرفت.
ایمنی مواد شیمیایی بهعنوان یکی از چالشهای رایج در محیطهای صنعتی، با محوریت برچسبگذاری، برگههای اطلاعات ایمنی (SDS)، روشهای نگهداری، حملونقل و واکنش اضطراری به نشت یا تماس بررسی شد. در ادامه، ایمنی ماشینآلات و اهمیت نصب حفاظها، کنترلهای اضطراری، آموزش کاربر و برنامههای تعمیر و نگهداری ایمن مورد بحث قرار گرفت.
یکی از بخشهای مهم این مقاله، معرفی سیستم قفلبرچسبگذاری (LOTO) برای کنترل انرژیهای خطرناک هنگام تعمیرات و نگهداری بود که بهعنوان یکی از مؤثرترین روشهای پیشگیری از راهاندازی ناخواسته ماشینآلات شناخته میشود. در بخش پایانی نیز ایمنی کار در ارتفاع و الزامات استفاده از تجهیزات حفاظت فردی (PPE)، سیستمهای مهار سقوط و آموزشهای مرتبط بررسی گردید.
در مجموع، اجرای مؤثر برنامههای ایمنی صنعتی نیازمند تعهد مدیریت، مشارکت کارکنان، آموزش مستمر، استفاده از تجهیزات مناسب و فرهنگسازی ایمنی است. هدف نهایی آن است که محیطهای کاری ایمنتر، بهرهورتر و انسانیتر ساخته شوند؛ جایی که سلامت نیروی کار، سرمایهای بیبدیل تلقی شود.